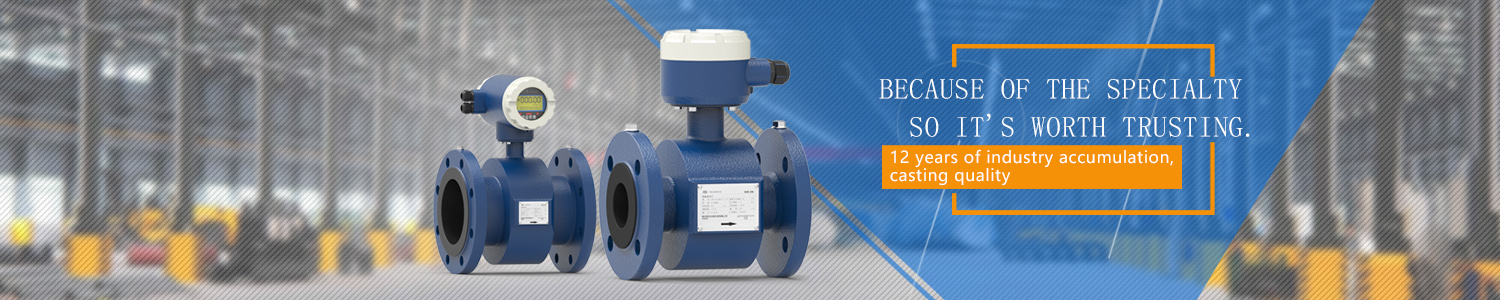
Analysis of fault cause of field instrument
Every instrument manufacturer, including our south control instrument, cannot guarantee that every instrument sold can achieve zero fault, which is related to the construction of the instrument and the operating habits of field operators.Therefore, the overhaul of the meter is also essential, it is a tedious and very patient thing.
When analyzing the fault cause of field instrument, special attention should be paid to the characteristic change of control object and control valve, which may be the cause of the fault of field instrument system.Therefore, we should take comprehensive consideration and careful analysis from the two aspects of the field instrument system and the process operating system to check the cause. The measurement parameters of the field instrument are generally divided into four parameters: temperature, pressure, flow rate and liquid level.
First, before analyzing and checking the fault of the field instrument system, the operator should be informed of the changes of load and raw material parameters in production, check the recording curve of the fault instrument, and make a comprehensive analysis to determine the cause of the fault of the instrument.
Secondly, before analyzing the fault of the field instrument system, the design scheme and design intention of the instrument system should be thoroughly understood, including the structure, characteristics, performance and parameter requirements of the instrument system, production process, production process and conditions of the related instrument system.
Ⅰ、Failure analysis of flow control instrument system
The indicator value of the flow control instrument system reaches the minimum hour. First check the field instrument.When the field instrument indication is also minimal, check the valve opening, if the valve opening is zero, it is usually the fault between the regulator and the regulator.When the field test instrument indicates the minimum, the regulating valve is open normally, and the fault is probably caused by the system pressure is not enough, the digital display control instrument system pipeline is blocked, the pump is not up, medium crystallization, improper operation and other reasons.If the fault of the instrument is caused by the following reasons: the orifice differential pressure flowmeter may be the catheter plug under positive pressure.Positive pressure chamber leakage of differential pressure transmitter;Mechanical flowmeter is a gear stuck or blocked screen.
When the indicator value of the flow control instrument system reaches the maximum, the detection instrument will usually indicate the maximum value.At this point, the valve can be opened or closed manually remote control, if the flow rate can fall down generally for the process operating reasons.If the flow value does not fall, it is the cause of the instrument system, check whether the regulating valve of the flow control instrument system ACTS;Check the instrument to measure whether the pressure system is normal;Check the instrument signal transmission system is normal.
The indicator value of the flow control instrument system fluctuates frequently, and the control can be changed to manual. If the fluctuation is reduced, it is because of the instrument or the improper PID of the instrument control parameter. If the fluctuation is still frequent, it is because of the process operation.
Ⅱ、Fault analysis of liquid level control instrument system
The indicator value of the liquid level control instrument system changes to the maximum or minimum, you can check the instrument first to see if it is normal. If the indicator is normal, change the liquid level control to manual remote control level to see the liquid level change.If the liquid level can be stable in a certain range, the fault in the liquid level control system;If the liquid level cannot be stabilized, it is usually the fault caused by the process system. The reason should be found from the process aspect.
If the indicator of the differential pressure level control instrument and the field direct reading indicator are not correct, first check whether the field direct reading indicator instrument is normal. If the indicator is normal, check whether the negative pressure pipe sealing liquid of the differential pressure level instrument has leakage.If leakage occurs, refill the sealing liquid and adjust the zero;No leakage, it may be that the negative migration of the meter is wrong, and adjust the migration to make the meter normal.
When the indicator value of the liquid level control instrument system changes and fluctuates frequently, the capacity of the liquid level control object should be first analyzed to analyze the cause of the fault.The small capacity of the first to analyze whether there are changes in the process operation, if there are changes are likely to be the process caused by frequent fluctuations.If no changes may be due to instrument failure.
If the user encounters the problem of abnormal display in the process of using, it is bound to be troublesome, but careful investigation can always find the root of the problem.South control instrument for the majority of users on - site use inspection, will do its best for your service.