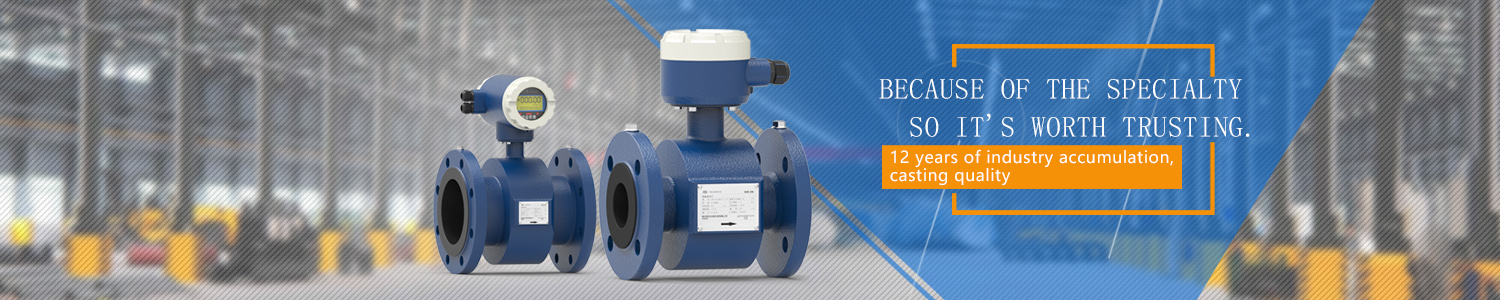
Liquid flowmeter fault self-test
Ⅰ.LWGY series turbine flow meter is a new generation of turbine flow meters which has absorbed the advanced technology of flow meter at home and abroad,and is manufactured according to JB/9246-199 standard. It has the characteristics of simple structure, light weight, high precision, good reproducibility, high responsiveness, easy installation and maintenance.
Ⅱ. Maintenance:
1)Always observe whether the sensor power cable and transmission cable (or wire) are damaged or aging, and protect the rubber sheath outside the cable.
2)Regularly (generally half a year) use soft non-scrubbing electrode surface to remove dirt or sediment.
3)Remove sundries in the upstream channel of the sensor.
Ⅲ.Faults and troubleshooting
1) The liquid does not flow and has an output: 1. There is an open circuit connection between the signal transmission cable and the converter; 2. The signal cable is disconnected from the electrode connection; 3. The surface of the electrode is contaminated or deposited with an insulating layer; 4. The grounding is poor or the circuit is broken.
Solution: 1. Connect the cable; 2. Open the sensor, reconnect it; 3. Scrub the electrode surface; 4. Connect the bottom line.
2) No flow of liquid flow: 1. The two transmission wires of the signal transmission cable between the converter and the converter are reversed; 2. The power supply is not connected or the contact is poor; 3. The sensor has leaks in the pipe, the outer casing and the end face.
Solution: 1. Rewind the head; 2. Connect the power supply and keep the contact well; 3. Repair the sensor.
3) The output is unstable: 1. The flow field is unstable; 2. The liquid passing through the sensor contains gas, large solid block; 3. The electrical connection is virtual; 4. The grounding is poor; 5. The electrode leaks.
Solution: 1. Transform the channel, or increase the installation of fake sensors; 2. Normal phenomenon; 3. Check the wiring, connect the line; 4. Connect the ground wire 5. Repair the sensor.
4) The error is too large: 1. The zero point is too high; 2. The liquid is not completely filled; 3. The power supply is distorted too much; 4. The grounding is poor.
Solution: 1. Re-adjust the zero point; 2. Improve the channel conditions, the sensor is always full of liquid; 3. Improve the power supply conditions, in line with normal working conditions; 4. Connect the ground wire.