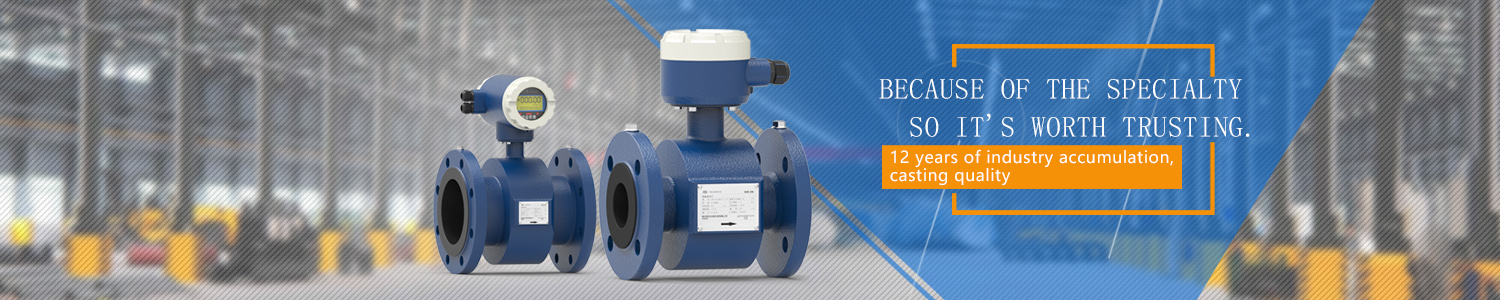
Blog Categories
Recent Posts
Analysis of the reasons for the decrease of turbine flowmeter accuracy
1, there are some impurities in the medium, the bearing, the shaft to wear, so that the gap between the two increase, the dynamic balance of the moving parts is destroyed, rotational speed decline, or dirt into the clearance, so that the motion resistance increase, rotational speed decline.All these cause the decrease of instrument display value and negative error, which is unfavorable to the fluid supplier.
2. Fibrous or viscous impurities in the fluid are attached to the rotating part of the flowmeter, which will increase the rotational resistance and cause the indicating value of the meter to decrease, resulting in negative error, which is unfavorable to the fluid supplier.
3, fluid temperature and pressure changes may make the escape of the liquid in the pipe air or because of the pressure inside the pipeline is lower than fluid saturation vapor pressure, make part of the liquid and steam, is also likely to make out with medium pressure air is sucked into the pipe, the gas with the measured liquid, causing instrument indicated value increase, there is error, adverse to the fluid of the buyer.
4. Poor working environment, such as electromagnetic interference, dust, high temperature, vibration, humidity, etc., may cause wrong operation or failure of turbine flow sensor, which directly leads to the indicating error of turbine flowmeter. The error may be positive or negative, which may not be obvious, or may be completely ineffective.For the above phenomenon, when it is more serious, problems can be found from the comparison of the working status of the process, and it is easy to take corresponding measures.But at the beginning of a problem, you can't find it without taking special measures.
Attention should be paid to the maintenance of turbine flowmeters:
1. When used, the tested medium should be kept clean and free of impurities such as fibers and particles.
2. When the turbine flow sensor is first used, slowly fill the medium inside the sensor, and then open the outlet valve (the valve should be installed at the back end of the flowmeter). It is strictly prohibited for the sensor to be impacted by high-speed fluid when it is in a medium-free state.
3. The maintenance cycle of turbine flow sensors is generally half a year.When repairing and cleaning, please pay attention not to damage the parts in the measuring chamber, especially the impeller.Please pay attention to the position relation of guide parts and impeller during assembly.
4. When the turbine flow sensor is not in use, the internal media should be cleaned. After blow-drying, protective covers should be put on both ends of the sensor to prevent grime from entering, and then stored in a dry place.
Related products: precession vortex flow meter, roots flow meter