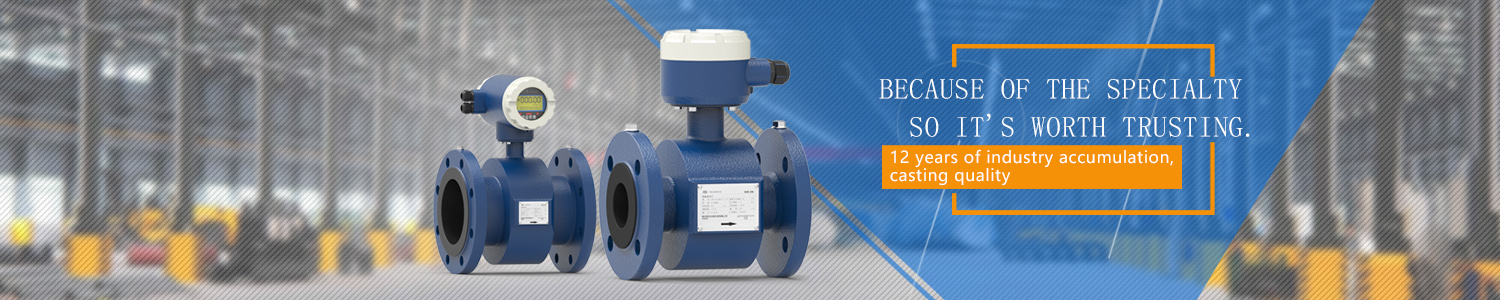
Blog Categories
Recent Posts
How to analyze the fault of instrument on site with different parameters?
1、Fault analysis of flow control instrument system
(1)When the indication value of flow control instrument system reaches the minimum, firstly check the on-site detection instrument. If it is normal, the fault will be displayed on the instrument.When the field test instrument indicator is also the smallest, check the valve opening, if the valve opening is zero, it is often a fault between the regulator and the regulator.When the field test instrument indicates the minimum, the valve opening is normal, the fault is likely to be the system pressure is not enough, digital display controller system pipe blockage, pump does not load, medium crystallization, improper operation and other reasons.If the instrument fault, the reasons are: orifice differential pressure flowmeter may be positive pressure guide pipe plug;Leakage of positive pressure chamber of differential pressure transmitter;Mechanical flowmeter is gear stuck or blocked screen, etc.
(2)When the indication value of flow control instrument system reaches the maximum, the detection instrument will often indicate the maximum.At this point, the manual remote control valve can be opened or closed small, if the flow can be down for the general reasons of process operation.If the flow value does not come down, it is the cause of the instrument system, check whether the flow control instrument system of the control valve action;Check whether the gauge pressure guiding system is normal;Check whether the instrument signal transmission system is normal.
(3)The indicator value of flow control instrument system fluctuates frequently, the control can be changed to manual, if the fluctuation decreases, it is the cause of the instrument or the instrument control parameter PID is not appropriate, if the fluctuation is still frequent, it is caused by the process operation.
2、Fault analysis of liquid level control instrument system
(1)The indicator value of the liquid level control instrument system changes to the maximum or the minimum, you can first check the detection instrument to see whether it is normal, such as normal instructions, the liquid level control to manual remote control liquid level, see the liquid level change.If the liquid level can be stable in a certain range, the fault is in the liquid level control system;If not stable liquid level, generally for the process system caused by the fault, to find the reason from the process.
(2)When the indicator of the differential pressure level control instrument and the field direct reading indicator cannot be matched, firstly check whether the field direct reading indicator is normal. If the indicator is normal, check whether the sealing liquid of the negative pressure guide pressure pipe of the differential pressure level instrument is leaking.If there is leakage, refill the sealing fluid and adjust the zero point;No leakage, may be the instrument of negative migration is wrong, readjustment of migration so that the instrument indicator is normal.
(3)When the indicating value of the liquid level control instrument system fluctuates frequently, the volume of the liquid level control object should be analyzed first to analyze the cause of the fault.Small capacity to analyze whether there is a change in the operation of the process, if there is a change is likely to be frequent fluctuations caused by the process.If there is no change, it may be caused by instrument failure.
3、Fault analysis procedure of temperature control instrument system
When analyzing the fault of temperature control instrument system, two points should be paid attention to firstly: the instrument of this system mostly adopts electric instrument to measure, indicate and control;The measurement of the system instrument often lags behind.
(1)The indication value of temperature instrument system suddenly changes to the maximum or minimum, which is usually a fault of instrument system.Because the temperature meter system measurement lag is large, there will be no sudden change.At this time, the fault is caused by thermocouple, thermal resistance, compensation wire breakage or transmitter amplifier failure.
(2)The temperature control instrument system indicates rapid oscillation, which is mainly caused by improper PID adjustment of control parameters.
(3)The indication of temperature control instrument system shows a large and slow fluctuation, which is probably caused by the change of process operation. If there is no change of process operation at that time, it may be the fault of instrument control system itself.
(4)Fault analysis steps of the temperature control system itself: check whether the input signal of the control valve changes, the input signal does not change, the control valve action, the control valve diaphragm head leakage;Check whether the input signal of the valve locator changes, the input signal does not change, the output signal changes, the locator has a fault;Check whether the input signal of the locator has changed, and then check whether the output of the regulator has changed. If the input of the regulator does not change and the output changes, it is the fault of the regulator itself at this time.
4、Fault analysis of pressure control instrument system
(1)When the pressure control system instrument indication appears the rapid oscillation fluctuation, first checks whether the process operation has the change, this kind of change is mostly the process operation and the regulator PID parameter adjustment is not good causes.
(2)Instrument appear dead line pressure control system, technological operation changes the pressure indicator or not, the general failure occurs in the pressure measurement system, check first whether the measurement system for pressure pipe plugging phenomenon, not plugging, check whether there is any change on pressure transmitter output system, have change, the fault in the controller measurement indicator system.
The above is only the field fault analysis of the four common parameters of the field separate control instrument, and there are some complex control loops in the actual field, such as cascade control, range control, program control, interlocking control and so on.The analysis of these faults is more complex, to be specific analysis.
Solution: Exclusion method
1.When the system is under control, the judgment should also be the same. It is easy to find out the problem if the fault is judged after each part is independent.
2.It is only the instrument displayed on the spot, and it is suspected that the display data is abnormal. It can estimate the data according to the process environment. If the data are too far away, it is ok to just check and adjust the instrument.
3.If the field control instrument suspects that the display data is abnormal, it can automatically detach, observe and fix the data of process conditions, and determine whether the collected data is normal.If the control results are unstable, first determine whether the data collection is normal, the method is the same as above, because the data collection is not normal, the control results must not be.
The above problems are judged. When the soft manual output is checked, whether the actuator is in normal operation.Finally, adjust PID parameters.